Evolution of Boston Dynamics’ Atlas Robot
The Atlas robot has undergone significant transformations since its inception. Initially, Boston Dynamics introduced a hydraulic version of Atlas, creating a machine capable of remarkable feats, such as lifting heavy objects and traversing intricate terrains. This early model laid the groundwork for later enhancements.
With each iteration, engineers focused on improving mobility, strength, and dexterity. The new fully electric Atlas stands as a testament to this continuous innovation. The switch from hydraulics to electric power was driven by the desire for greater efficiency and functionality in real-world applications.
One noteworthy advancement is Atlas’ enhanced range of motion. The electric model features greater agility and the ability to perform tasks that were once unimaginable. This makes it not just a theoretical exercise but a practical tool ready for deployment in various industries, including automotive manufacturing, in collaboration with Hyundai.
Boston Dynamics didn’t stop with hardware improvements. Incorporating new AI and machine learning capabilities, the robots can now adapt to changing environments and tasks. Through reinforcement learning and computer vision, these robots tackle complex real-world situations with newfound efficiency.
The use of AI has also been expanded with the introduction of Boston Dynamics’ Orbit™ software. This platform streamlines the management of robot fleets, allowing for seamless integration of Spot, Stretch, and Atlas into enterprise environments. It provides a unified solution to handle site maps, operational data, and overall robot performance.
The focus on bipedal robots stems from the goal to develop machines that mimic human movement. Initially designed to move like humans, Atlas has evolved to surpass human capabilities in many aspects. The electric Atlas can execute intricate maneuvers, offering unprecedented levels of support in industrial settings.
The partnership with Hyundai for testing the new Atlas model highlights the practical applications of this advanced robot. This collaboration will provide valuable insights into how Atlas performs in real-world manufacturing environments, paving the way for more widespread use.
In addition to the advancements in mobility and AI, Boston Dynamics has worked on improving the robot’s hardware. New gripper variations are being explored to handle diverse tasks, reflecting the increasing intricacy of jobs Atlas can undertake.
This shift from R&D to practical applications marks a significant milestone for Boston Dynamics. The company’s track record with Spot and Stretch shows that they can deliver robots that bring real value to customers, not just in theory but also in practice.
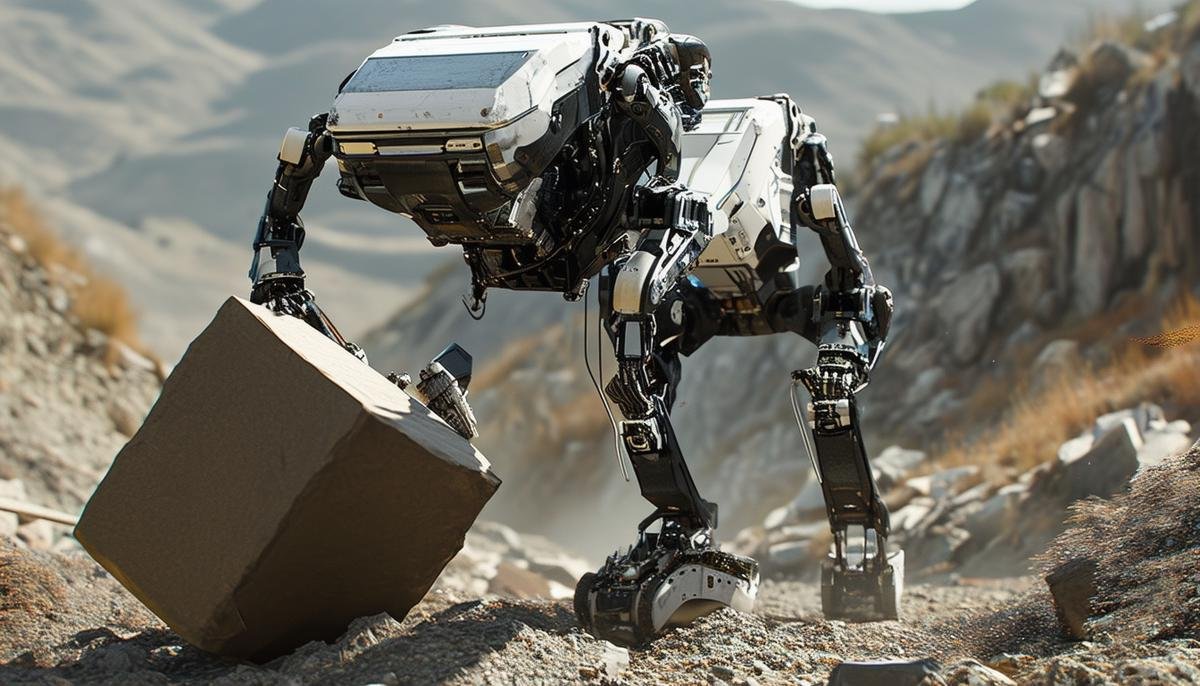
Real-World Applications of Atlas
The next phase for the electric Atlas is to illustrate its real-world applications. One primary sector where Atlas is expected to make a significant impact is in industrial settings. With its enhanced agility and strength, Atlas is well-positioned to handle demanding tasks in environments that were previously challenging for robots.
In the manufacturing sector, Atlas can assist in operations that require precision and flexibility. For instance, production lines that involve handling intricate and irregularly shaped components can benefit greatly from Atlas’ advanced gripper systems and dexterous movement capabilities. The robot’s improved range of motion allows it to maneuver in tight spaces and perform tasks that typically require human intervention, effectively reducing the risk of injury and increasing productivity.
The partnership with Hyundai exemplifies the robot’s potential in automotive manufacturing. Hyundai’s involvement provides an ideal testing ground for Atlas’ capabilities. The collaboration aims to explore how Atlas can be integrated into the automotive production line, performing tasks such as:
- Assembling intricate parts
- Managing logistics within the plant
- Conducting quality control checks
By leveraging Atlas’ capabilities, Hyundai anticipates improvements in production efficiency, safety, and overall operational effectiveness.
Beyond manufacturing, Atlas has the potential to revolutionize other sectors as well. In warehousing, for example, the deployment of Atlas can result in better inventory management and streamlined operations. It can assist in loading and unloading goods, handling materials that vary in size and weight with ease. This adaptability reduces downtime and enhances throughput, contributing to more agile supply chains.
Atlas is poised to make significant contributions in sectors like construction, where the environment is often unpredictable and hazardous. The robot’s ability to traverse uneven terrains and lift heavy objects while maintaining stability is invaluable. By taking on tasks such as site inspections, carrying materials, and assisting with assembly, Atlas can alleviate the burden on human workers and contribute to safer and more efficient construction projects.
The healthcare sector is another area where Atlas could have a meaningful impact. In settings such as hospitals, Atlas could support tasks that require a high level of precision and reliability, such as delivering supplies, assisting in surgeries, or providing support in rehabilitation exercises. By handling these roles, Atlas allows healthcare professionals to focus on more critical aspects of patient care, ultimately enhancing the overall quality of service.
The agriculture industry also stands to benefit from the capabilities of Atlas. The robot can be deployed for planting, harvesting, and performing quality checks, ensuring that agricultural processes are more efficient and less labor-intensive. This can lead to higher crop yields and reduced wastage, addressing some of the key challenges faced by the industry.
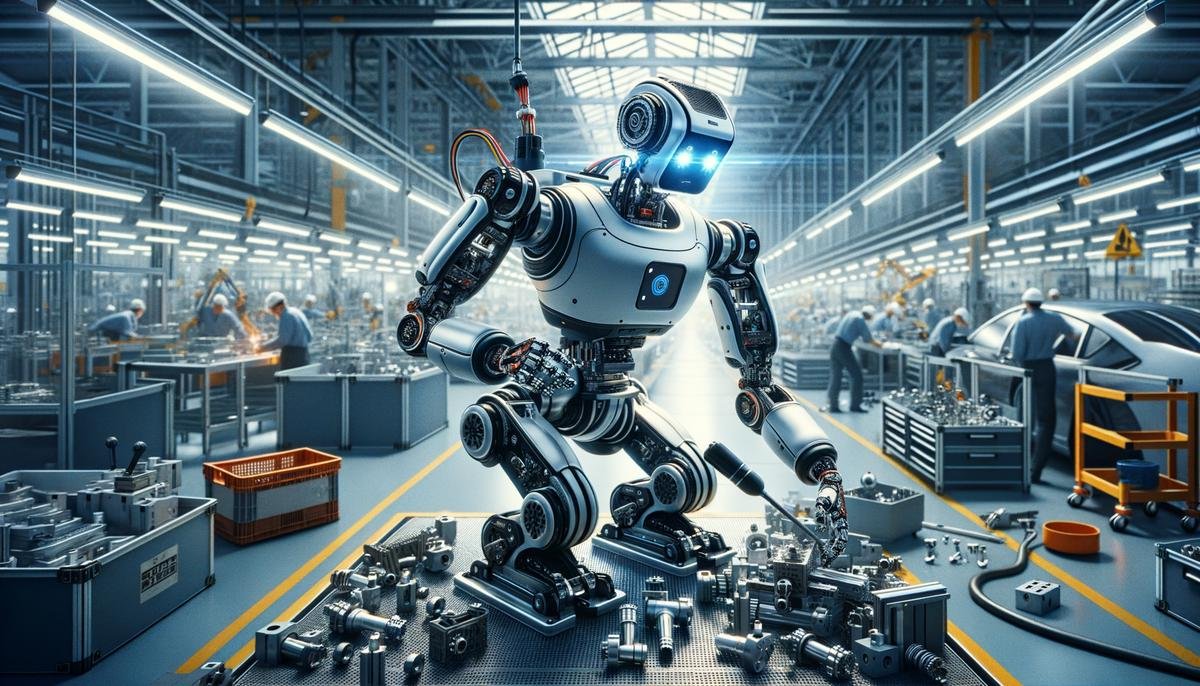
Integration of AI and Machine Learning
Incorporating AI and machine learning technologies has been a game changer for Boston Dynamics’ robots, significantly enhancing their capabilities and adaptability. One of the standout techniques employed is reinforcement learning. This approach allows robots to learn from their actions and improve over time. By interacting with the environment and receiving feedback, robots can eventually understand the best way to accomplish tasks, adapting to new conditions with impressive agility.
Reinforcement learning has been particularly integral in teaching robots to traverse intricate terrain and perform complex tasks independently. For instance, in industrial settings, a robot can learn to avoid obstacles, recognize different objects, and choose the most efficient path to complete its assignment. This learning process is akin to how animals and humans learn through trial and error, except here, it happens at an accelerated pace thanks to advanced algorithms and computational power.
Another critical component of Boston Dynamics’ AI arsenal is computer vision. This technology equips robots with the capability to interpret and understand visual information from the world around them. Through computer vision, robots can detect objects, recognize patterns, and make informed decisions based on visual input. For example, in logistics, robots can identify and sort packages based on labels and dimensions, drastically improving sorting accuracy and efficiency.
By integrating computer vision with reinforcement learning, Boston Dynamics has created robots that can handle unpredictable environments with higher precision and efficiency. This combination is particularly beneficial in sectors like agriculture, where robots might need to traverse uneven fields and identify specific crops for harvesting.
Adding to these AI technologies is Boston Dynamics’ Orbit™ software, a centralized platform designed to manage robot fleets efficiently. Orbit™ serves as the operational backbone for deploying and overseeing multiple robots, including Spot, Stretch, and the new electric Atlas. By providing a unified interface, this software simplifies the coordination of tasks, tracks robot performance, and ensures that operations run smoothly.
Orbit™ also allows for the creation of digital twins—virtual replicas of physical environments. By using data gathered from robots like Spot, these digital twins offer detailed models of facilities, enabling better planning and execution of tasks. Imagine a manufacturing plant where a digital twin mirrors the real-world environment, allowing engineers to simulate and optimize processes before implementation. This feature ensures that the robots are well-prepared for real-world scenarios, reducing downtime and increasing operational efficiency.
The integration of machine learning is not just about making robots smarter, but also about making them adaptable. Boston Dynamics’ use of neural networks enables robots to learn from vast datasets, continuously enhancing their problem-solving abilities. This adaptability is crucial for applications in dynamic environments, such as disaster management, where conditions can change rapidly and unpredictably.
Lastly, the continuous feedback loop enabled by these technologies ensures that Boston Dynamics’ robots are not static entities but evolving tools capable of tackling increasingly complex tasks. This evolution is particularly evident in the healthcare industry, where robots are being developed to assist with intricate surgical procedures, offering precision and control that surpass human capabilities.
Spot and Stretch: Complementary Robotics Solutions
In Boston Dynamics’ product lineup, Spot and Stretch play complementary roles alongside the advanced Atlas robot, forming a multifaceted robotics ecosystem capable of catering to various industrial needs.
Spot, the agile quadruped robot, has been designed to traverse challenging terrains that are typically inaccessible to traditional wheeled robots. Ideal for inspections, data collection, and surveillance, Spot excels in environments like:
- Oil and gas facilities
- Construction sites
- Power plants
Its ability to traverse stairs, rocky landscapes, and other obstacles allows it to perform operational tasks that prioritize safety and efficiency. The agility of Spot ensures that it can access and inspect areas that would otherwise endanger human workers, capturing high-quality data that informs critical decision-making processes.
In industrial settings, the inclusion of Spot provides an added layer of operational efficiency. For example, Spot is equipped with custom payloads, such as 360-degree cameras and environmental sensors, to monitor site conditions continuously. This capability is pivotal for predictive maintenance, where early detection of anomalies can prevent costly downtimes and enhance overall productivity. Additionally, Spot’s adaptability makes it a perfect tool for creating digital twins—virtual models of physical environments—by scanning facilities and feeding accurate data into Boston Dynamics’ Orbit™ software. This synergy between Spot’s on-ground capabilities and Orbit™’s data processing enables modeling and simulation for process optimization.
Where Spot brings agility and precision in traversing complex terrains, Stretch serves a different but equally important function in logistics and material handling operations. Designed to enhance warehouse efficiency, Stretch focuses on automating repetitive, labor-intensive tasks such as case handling and trailer unloading. Its powerful robotic arm, combined with advanced vision systems and an AI control platform, ensures that Stretch can handle a wide variety of packages with speed and accuracy.
Stretch’s role in the robotics ecosystem is particularly important in addressing the challenges of modern warehousing, where the sheer volume of goods and the speed of turnaround demand highly efficient solutions. Stretch can pick and place objects of various sizes and shapes, facilitating the smooth transition of goods through the supply chain. By automating these repetitive tasks, Stretch reduces the physical strain on human workers, enabling them to focus on higher-value activities that require critical thinking and problem-solving skills.
The complementary nature of Spot and Stretch becomes even more evident when integrated into the broader operational workflow. While Spot can provide real-time environmental data and perform inspections, Stretch can simultaneously optimize the flow of materials within the facility. This combination enhances both the safety and efficiency of industrial operations. For instance, in a warehouse setup, Spot could conduct regular inspections to ensure the safety and operational integrity of the facility, while Stretch manages the logistics of moving goods, thereby creating a seamless, interconnected workflow.
The implementation of these robots showcases Boston Dynamics’ commitment to providing versatile, scalable solutions tailored to specific industrial challenges. As with Atlas, the integration of AI and machine learning enhances the capabilities of Spot and Stretch. For example, Spot’s computer vision and autonomous navigation ensure that it can operate efficiently in dynamic, unpredictable environments. Similarly, Stretch’s advanced vision systems and AI algorithms allow it to adapt to various packaging formats and operational layouts, making it a versatile tool for a range of logistics applications.
Together, Spot, Stretch, and Atlas form a cohesive suite of robotics solutions that can revolutionize industrial operations. The sophisticated capabilities of Atlas in performing complex, bimanual tasks, combined with Spot’s agility in traversing challenging terrains and Stretch’s efficiency in material handling, create a formidable trio. This synergy not only improves individual task execution but also enables a comprehensive approach to industrial automation.
By integrating these robots, organizations can build more resilient, efficient, and safer operations. The robots don’t just operate in isolation but work together, seamlessly integrating their unique capabilities to create a balanced and optimized workflow. This holistic approach maximizes the potential of robotics technology and paves the way for smarter, more responsive industrial environments.
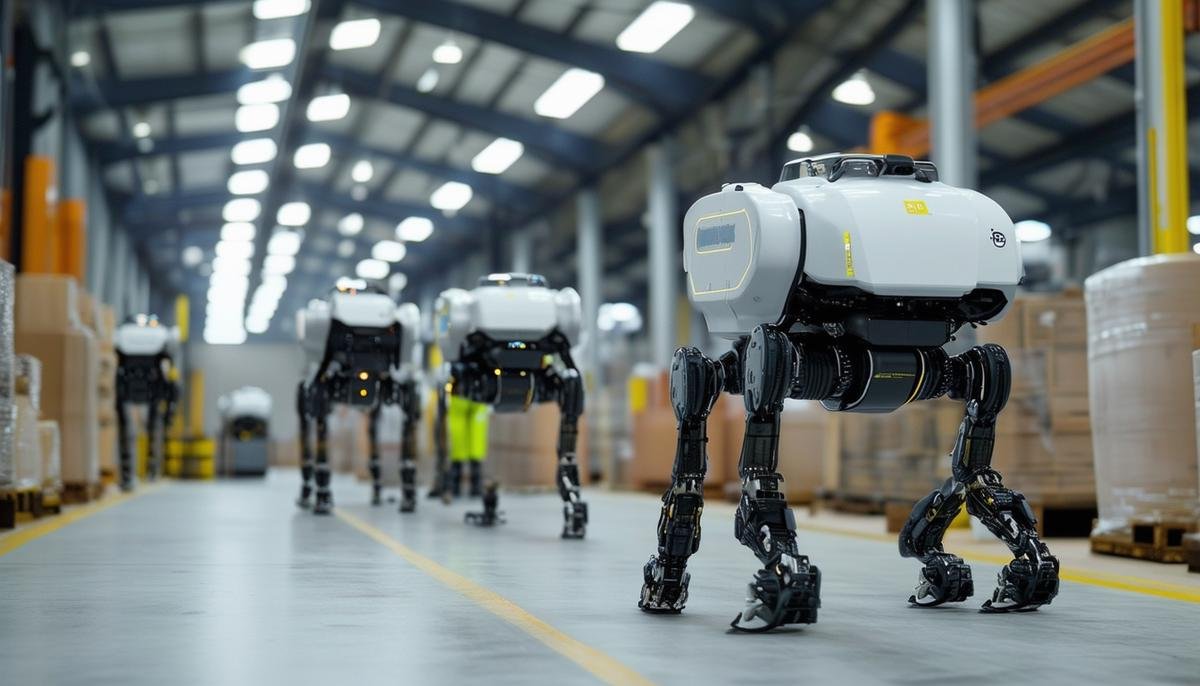
Boston Dynamics AI Institute
The Boston Dynamics AI Institute, launched with an initial investment of over $400 million, aims to push the boundaries of AI, robotics, and intelligent machines. Led by Marc Raibert, the founder of Boston Dynamics, the Institute focuses on three primary areas:
- Cognitive AI: Improves the decision-making and problem-solving abilities of robots, enabling them to perform tasks that require higher-level thinking and adaptation.
- Athletic AI: Refines the physical capabilities of robots, making them more agile, precise, and effective at interacting with their surroundings.
- Organic hardware design: Creates innovative and adaptable physical components for robots that integrate seamlessly with the software systems driving robotic behavior.
The Institute collaborates with Hyundai Motor Group to develop advanced robots capable of tackling real-world challenges. This partnership merges Boston Dynamics’ pioneering robotics technology with Hyundai’s vision of transforming automotive manufacturing and beyond.
The institute also collaborates with leading universities and corporate research labs to accelerate progress in its core technical areas. This multidisciplinary approach attracts talent from diverse fields, contributing to a rich ecosystem of innovation. The Boston Dynamics AI Institute is committed to ethical considerations in AI and robotics, ensuring that the development and deployment of advanced robots align with societal values and contribute positively to human well-being.
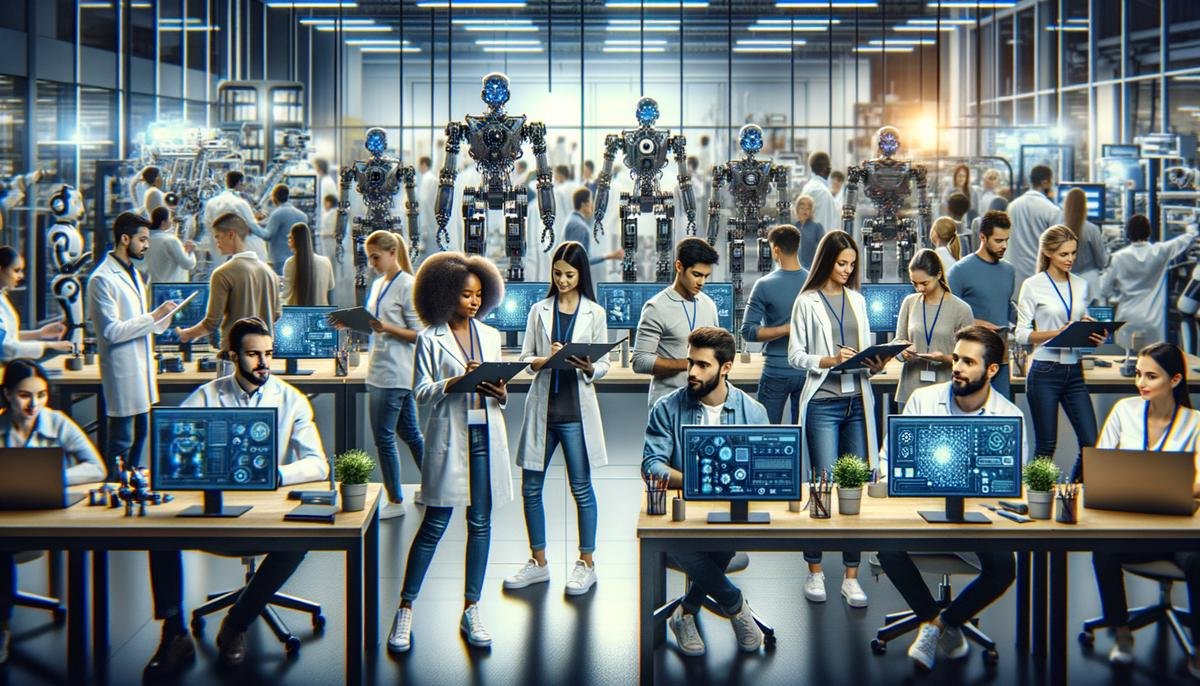
Future Prospects and Challenges
Boston Dynamics’ robotics innovations have exciting future prospects, with potential applications in sectors such as agriculture, healthcare, aerospace, and electronics. However, realizing these prospects comes with challenges.
Technical hurdles include developing robots that can operate reliably in diverse, unstructured environments. Economic factors, such as the high cost of development, production, and maintenance, can be a barrier for widespread adoption. Integration of robots into existing workflows and industry standards requires investment in workforce training and fostering a culture that embraces new technologies.
Safety and regulatory compliance are essential, particularly for applications in healthcare and public spaces. Ethical considerations regarding privacy, job displacement, and the responsible use of AI must be addressed transparently.
Boston Dynamics must work closely with policymakers to create frameworks that ensure responsible innovation, balancing technological progress with societal impact. By collaborating with industry leaders, regulatory bodies, and academic institutions, Boston Dynamics is well-equipped to handle these challenges and drive the future of robotics forward.
The evolution of Boston Dynamics’ Atlas robot from its hydraulic beginnings to its current electric form showcases the progress in robotics and its potential impact across various industries. Atlas has demonstrated impressive capabilities, such as:
- Performing parkour and backflips1
- Navigating uneven terrain and obstacles2
- Manipulating objects with human-like dexterity3
These advancements in Atlas’s design and performance highlight the rapid development of robotics technology and its potential to revolutionize industries such as manufacturing, construction, and search and rescue operations.