Understanding Predictive Maintenance
Predictive maintenance is revolutionizing industrial equipment management. By leveraging data to anticipate machine issues before they escalate into serious breakdowns, companies can save substantial time and money. Industrial giants like GE are at the forefront of this transformation, utilizing platforms such as Predix AI to continuously monitor machine health, thereby minimizing unexpected disruptions and replacing costly emergency repairs with planned maintenance.
The technology powering predictive maintenance includes:
- Digital twins: Virtual representations of physical machines that allow operators to predict future operational health
- Advanced analytics: Algorithms that process vast amounts of data to derive actionable insights
By transforming collected data into actionable insights, industries can optimize operations. Sensors and machine learning models work in tandem to create an efficient ecosystem of machines and data, streamlining operations and boosting productivity.
For instance, GE Aerospace employs precise monitoring systems to track engine data continuously. When a sensor detects an unusual reading, maintenance teams can intervene promptly, averting major operational issues.
In the realm of inspection, AI-powered technologies are automating repetitive tasks. Advanced robotics and techniques like non-destructive X-ray fluorescence detect anomalies with unprecedented precision, facilitating targeted maintenance.
Companies are integrating AI into everyday operations to enhance inspection and repair processes. Tools like Proficy Solution assist in diagnosing performance issues and improving workflow by transforming raw data into decisive action points.
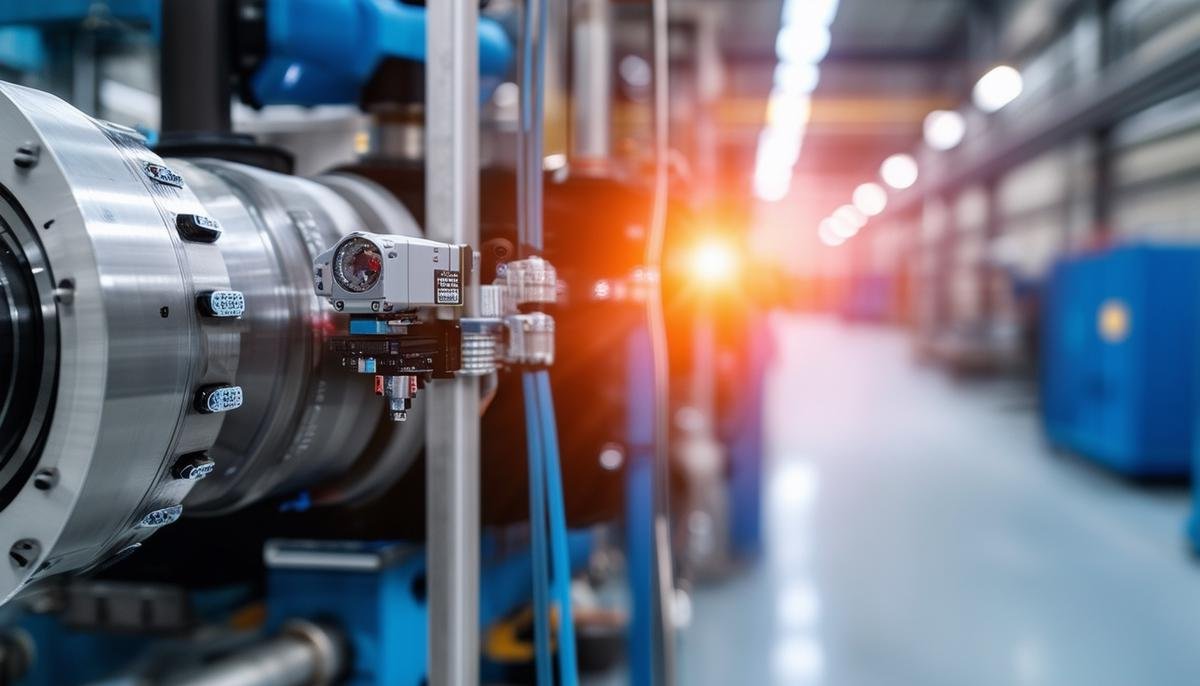
GE's Predix AI Platform
GE's Predix AI platform seamlessly integrates digital twins and real-time data analysis to anticipate equipment malfunctions. These digital twins, serving as virtual representations of physical assets, gather and translate data into comprehensible insights for equipment optimization.
The platform employs sophisticated machine learning algorithms that adapt and refine their strategies based on operational data. This approach enables a paradigm shift from traditional maintenance methods to predictive strategies that preempt disruptions.
Predix AI guides industrial operations toward enhanced maintenance regimens while minimizing human error. It dynamically adjusts maintenance plans in real-time based on current readings and insights, allowing for agile planning that responds to real-world conditions.
"We're on a learning journey, and we've got to make sure that our pace of learning keeps up with the pace that technology is evolving." – David Burns, CIO of GE Aerospace
The platform demonstrates particular efficacy in sectors where operational stakes are high, such as energy and aviation. In the aviation industry, for example, Predix's monitoring capabilities can predict potential issues with engine components, enabling maintenance crews to act preemptively and avoid costly failures.
By translating complex data into foresight, Predix AI empowers businesses to craft nimble and precise maintenance strategies. This ensures that industrial machinery operates efficiently and consistently, keeping pace with rapid technological advancements.
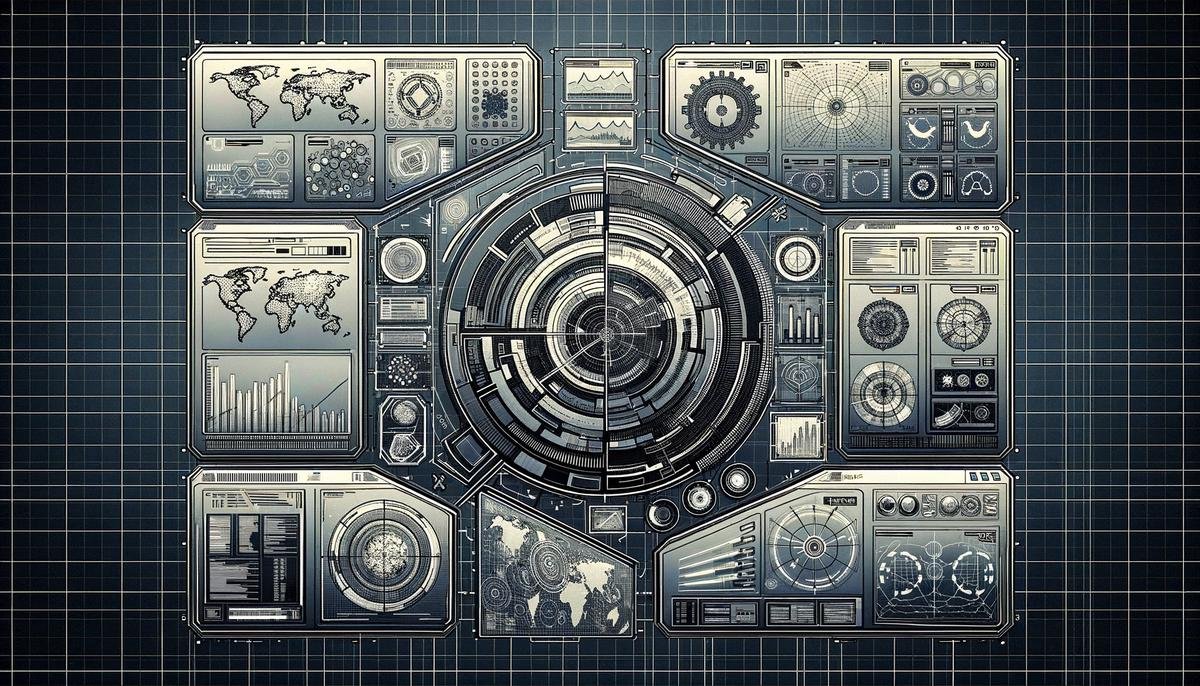
Applications in Various Industries
GE's Predix AI has far-reaching applications across diverse industries, enhancing performance and mitigating risks:
- Energy Sector: Provides insights into wind turbine health, allowing operators to address potential issues proactively, optimizing turbine uptime and increasing energy output.
- Aviation: Contributes to passenger safety by enabling precise timing of maintenance interventions. Constant data analysis uncovers subtle anomalies in engine operation, ensuring smooth flights and preventing unforeseen breakdowns.
- Manufacturing: Improves efficiency through digital twins that warn of potential mechanical issues, helping operators transition from crisis response to scheduled optimization.
- Oil and Gas: Utilizes smart process analytics to visualize data through time-series analysis, preventing costly drilling interruptions.
- Utilities: Employs grid analytics to predict outages, ensuring a resilient network capable of handling weather or consumption surges.
Across these industries, Predix AI provides foresight-driven solutions that enhance efficiency and reliability. It serves as an essential tool for businesses navigating modern market demands, offering data-informed insights that support decision-making and operational stability.
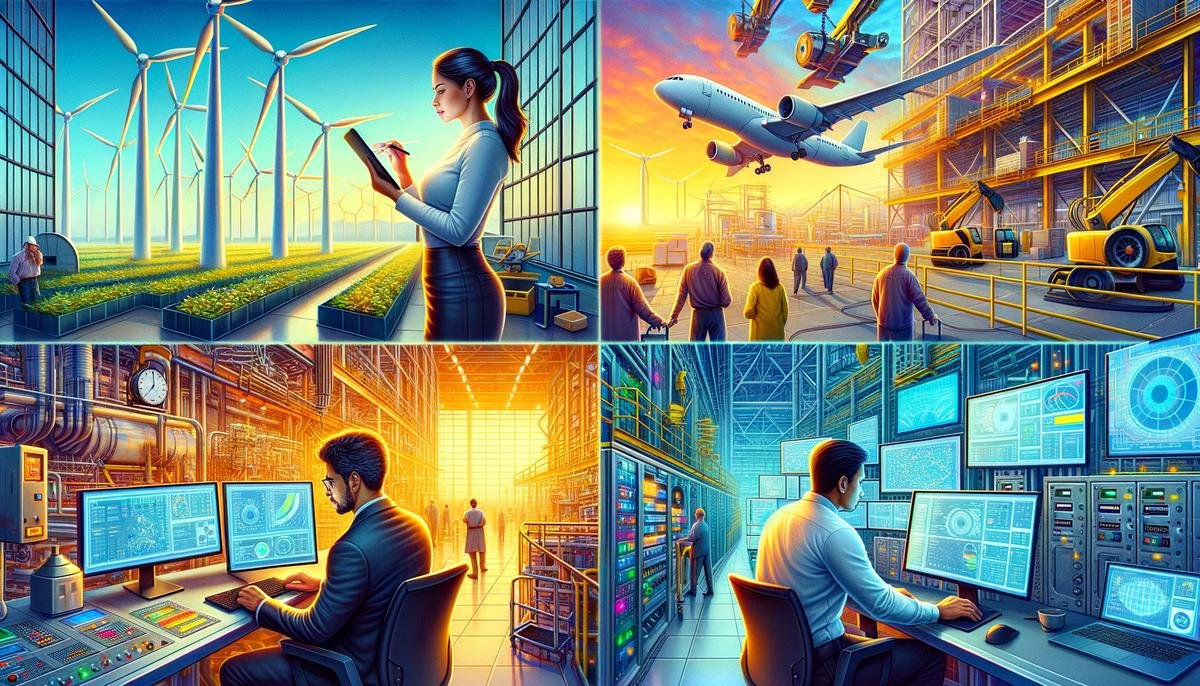
Benefits of SmartSignal Analytics
SmartSignal analytics offers several key benefits for predictive maintenance in industrial settings:
- Early Detection: Identifies equipment issues in their infancy, allowing for timely interventions before minor problems escalate into major malfunctions.
- Advanced Diagnostics: Utilizes advanced algorithms and digital twin technology to not only flag anomalies but also suggest potential causes, providing maintenance teams with a clear roadmap for problem-solving.
- Integrated Approach: Seamlessly integrates with GE Digital's broader suite of tools, transforming predictive maintenance from a reactive measure into a proactive strategy.
- Condition-Based Maintenance: Enables scheduling of maintenance based on actual conditions rather than fixed intervals, improving operational efficiency and reducing unplanned downtime.
- Cost Optimization: Allows businesses to prioritize maintenance actions based on predictive insights, fostering an operational environment that balances cost savings with performance enhancements.
SmartSignal's approach to asset management puts data at the forefront of decision-making. It combines early detection, detailed diagnostics, and strategic oversight to provide a comprehensive view of asset performance, offering industries a tool to meet maintenance demands with agility and precision.
"We chose SmartSignal to anticipate critical equipment failure before production disruption occurred because we knew it could scale to meet our needs and the visualization made it easy to see what actions we needed to take." – Matias Palacios, Rotating Equipment Engineer, Total EP
Future of AI in Predictive Maintenance
The future of AI in predictive maintenance promises increasingly sophisticated machine learning models capable of interpreting subtle patterns in data with unprecedented precision. These advancements could enable real-time optimization of asset performance, maintaining a competitive edge in rapidly evolving markets.
Digital twins are expected to evolve beyond simple digital representations, harnessing predictive analytics to simulate multiple operational scenarios. This capability will provide decision-makers with strategic intelligence to guide operations more effectively.
Increased automation in predictive maintenance may reduce the need for routine human inspections. AI-guided systems could handle routine maintenance adjustments, freeing skilled personnel to focus on higher-level problem-solving and innovation.
The integration of AI in predictive maintenance could foster deeper collaboration between suppliers and manufacturers. This networked approach to asset management could strengthen supply chains and promote industry-wide resilience.
As cognitive technologies advance, predictive maintenance may play a key role in achieving sustainability goals. By optimizing energy usage and extending machine lifecycles, the ecological footprint of industrial operations could be significantly reduced.
The future of AI in predictive maintenance aims to strike a balance between innovation and practicality. As this field matures, it promises to deliver precision, efficiency, and sustainability to ensure industry resilience in the face of evolving challenges.
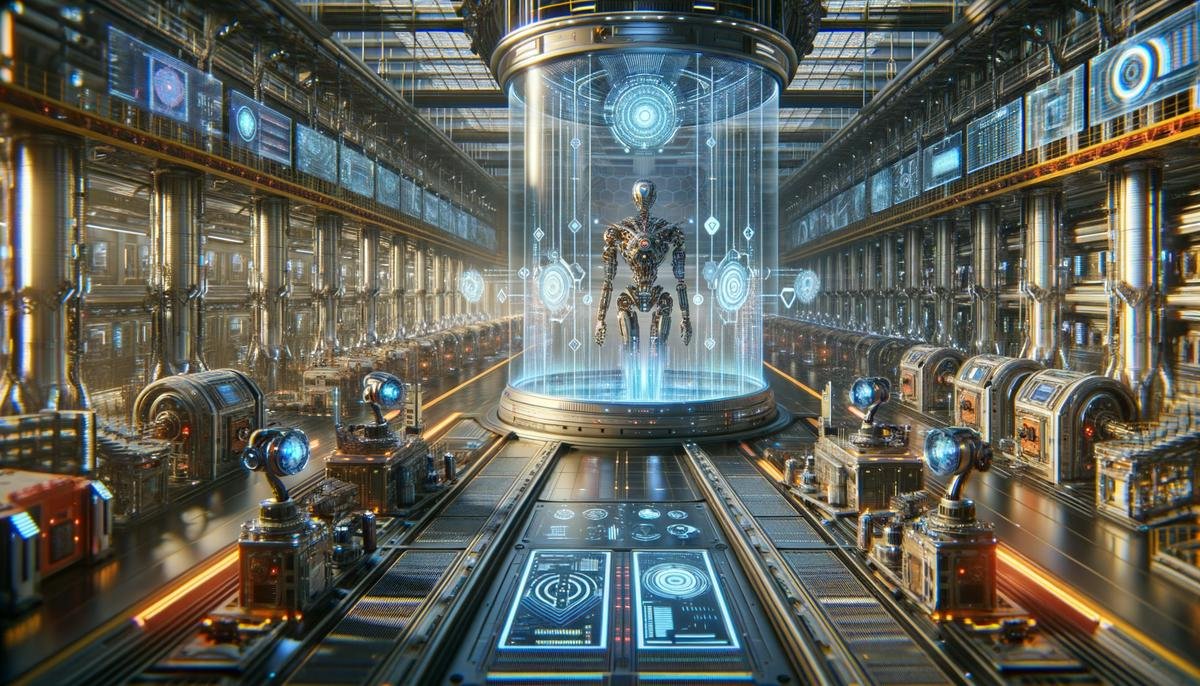
Predictive maintenance is reshaping industries by shifting from reactive to proactive strategies. This approach enhances operational efficiency and guards against unexpected disruptions, setting the stage for a future where foresight and precision guide industrial success.
- Burns D. GE Aerospace's AI Journey. GE Aerospace Press Briefing. 2023.
- Parris C. Digital Twin Development at GE. GE Digital Report. 2018.
- Shanbhag J. Predictive Maintenance in Aviation. GE Aerospace Customer Experience Report. 2023.
- Jenkins N. AI in Engine Inspections. GE Aerospace MRO Engineering Brief. 2023.
- Stokes R. AI and Robotics in Manufacturing Performance. GE Commercial Engines and Services Report. 2023.