As the sun rises on a new era of industrialization, the fusion of artificial intelligence with manufacturing signals a transformative leap in the way we produce, process, and perfect goods. At the heart of this revolution lies a rich tapestry of history and innovation that chronicles the ascent of AI from its nascent mechanical beginnings to the sophisticated orchestration of today’s smart factories. With this essay, we embark on a journey through the annals of AI in manufacturing, charting its evolutionary course and examining the intricate dance of man and machine that is reshaping the very fabric of production. As we delve into the current applications that define this dynamic field, we shed light on the complex intersection of technology, society, and economics, revealing how artificial intelligence is not just redefining the processes but also the possibilities of manufacturing.
History and Evolution of AI in Manufacturing
The Revolution of Artificial Intelligence in Manufacturing
In the epoch of rapid technological evolution, Artificial Intelligence (AI) has catalyzed a profound transformation in the manufacturing landscape. This metamorphosis is characterized by enhanced efficiency, precision, and customization, signifying a monumental leap from the traditional practices that once dominated production floors globally. AI has not only reshaped the processes but has also redefined the possibilities within the manufacturing realm.
Intelligent machines, equipped with AI, are capable of learning from experience. This ability to adapt and augment their functions has yielded unparalleled productivity. For decades, manufacturing was synonymous with extensive assembly lines where repetition and uniformity were the norm. However, with the analytical prowess of AI, systems can now predict and mitigate potential disruptions, forecast demand, and consequentially streamline production schedules.
Moreover, the integration of AI has mitigated human error, a once perennial challenge within the industry. Automated quality control implementation has substantially elevated the standard of products, invariably squelching the margin for defects and bolstering consumer trust. Precision is at the pinnacle of AI’s merits; it magnifies the capability to produce components with meticulous accuracy, a feat that was elusive in the pre-AI era.
One cannot ignore the advent of smart factories, the quintessence of AI’s influence. These facilities brim with sensors, Internet of Things (IoT) devices, and advanced robotics—all harmonized through AI. This advanced connectivity fosters an environment of real-time data analysis, enabling instantaneous adjustments and autonomous decision-making, thus streamlining operational efficiency. The consequential reduction in downtime and waste is a testament to AI’s transformative potential.
Customization, once a costly and time-intensive process, has been remarkably refined by AI technologies. With what is known as “mass customization,” AI allows for the production of tailored goods with virtually the same efficiency and speed as mass production. This has reinvented the consumer experience, allowing for personalized products that cater to specific preferences and requirements without exorbitant costs.
In summary, the maturation of artificial intelligence has ushered in an era of strategic manufacturing, where informed decision-making and meticulous execution reign supreme. The impacts of AI on the manufacturing landscape convey a resonating message: the factories of yesterday are not the factories of today or tomorrow. The technology continues to progress, and with it, the very fabric of manufacturing is continuously being woven into a more intelligent, efficient, and responsive industry. The culmination of AI’s journey within manufacturing is yet unwritten, but it is unequivocally guiding humanity towards a future where the lines between science fiction and industrial reality increasingly blur.

Current Applications of AI in Manufacturing
Continuing the exploration of Artificial Intelligence (AI) in the manufacturing industry, one must not overlook the significant strides made in supply chain optimization. AI systems are adept at analyzing vast swaths of data, leading to enhanced inventory management strategies. These strategies allow manufacturers to maintain optimal stock levels, reduce waste, and minimize storage costs, all while ensuring that production lines receive timely material replenishment.
Beyond supply chain management, AI is revolutionizing maintenance programs through predictive maintenance models. By continually monitoring equipment through sensors and data analytics, AI can anticipate when a machine is likely to fail or requires servicing, thus minimizing downtime and extending the life of manufacturing hardware.
In human-robot collaboration, AI-driven robots, known colloquially as cobots, work alongside human workers, enhancing safety and efficiency by taking over tasks that are either too dangerous, repetitive, or tedious for humans. This symbiotic relationship serves to not only preserve human ingenuity for complex decision-making but also to ensure that tasks can be conducted with unparalleled precision.
Manufacturing design is another key area wherein AI makes a notable impact. Utilizing generative design algorithms, AI can produce multiple iterations of a component or product design that optimizes for weight, strength, material usage, and cost, far beyond the capability of traditional design methods. Engineers can then evaluate these options against a set of criteria to identify the most efficient and economical design for production.
Lastly, AI plays a pivotal role in the training and support of employees within the manufacturing sector. Virtual reality (VR) and augmented reality (AR), powered by AI, provide immersive training experiences, allowing workers to learn new skills or understand complex machinery in a safe, controlled, and interactive environment. This training methodology effectively reduces errors and swiftly gets workers up to speed with evolving manufacturing processes.
These applications are but a snapshot of the breadth of AI’s integration in modern manufacturing, highlighting the profound influence this technology has on the nuances of production, design, and workforce development. The continued evolution of AI promises further refinement of these operations and paves the way for a manufacturing ecosystem that is progressively more intelligent, adaptable, and efficient.

Challenges and Limitations of AI in Manufacturing
Though the advancements in Artificial Intelligence (AI) proffer remarkable opportunities for the manufacturing sector, one must consider the challenges and limitations inherent in its implementation.
Firstly, the success of AI deployment in manufacturing processes hinges on the availability and quality of data. Data is the lifeblood of AI systems, and the effectiveness of algorithms is contingent on the volume, veracity, and velocity at which data is supplied. In the manufacturing context, the requisite granularity of data may often be lacking, and systems may need to grapple with ‘noisy’ or incomplete datasets, which in turn, can undermine the performance of AI applications.
Moreover, while adapting AI into manufacturing, integration with existing systems stands as a formidable challenge. Manufacturing entities often operate on legacy equipment and software that may not seamlessly interface with cutting-edge AI solutions, leading to potential disruptions and a need for significant investments in infrastructure upgrades or bespoke integration solutions.
The intricacies of AI necessitate a workforce that is proficient in these technologies—a criterion that is not easily met given the current skills gap. The labor force within the manufacturing industry must receive appropriate training to not only operate AI-driven systems but also to engage in their maintenance and improvement. The paucity of such skilled professionals can lead to an underutilization of AI capabilities.
Security and privacy are paramount concerns when implementing AI in manufacturing environments. The increasing connectivity required to harness AI, particularly in smart factories, exposes systems to cyber vulnerabilities, requiring robust security protocols to mitigate risks to intellectual property and sensitive data.
Another factor to consider is the ethical implications stemming from AI integration. AI systems might eventually lead to reduced human labor in certain tasks, which could affect employment rates and engender ethical dilemmas around the displacement of workers. Additionally, AI’s autonomy in decision-making necessitates careful consideration of the moral frameworks embedded within algorithms to avoid biases and ensure fairness.
Cost is a substantive factor that cannot be ignored. While AI has the potential to reduce costs in the long term through efficiencies and optimization, the initial investment required for implementing sophisticated AI technologies can be prohibitive for many manufacturing companies, particularly small and medium-sized enterprises (SMEs).
Lastly, regulatory and compliance issues present a challenge as the pace of AI development often outstrips that of policy and regulation. Ensuring compliance with existing regulations and anticipating future legal directives is crucial, but it can be resource-intensive and could slow down the speed of AI adoption.
In conclusion, the hurdles facing the adoption of AI in manufacturing are as complex as they are varied, involving technical, human, economic, and ethical factors. A nuanced approach that acknowledges these challenges is critical for realizing the full potential of AI in modern manufacturing.
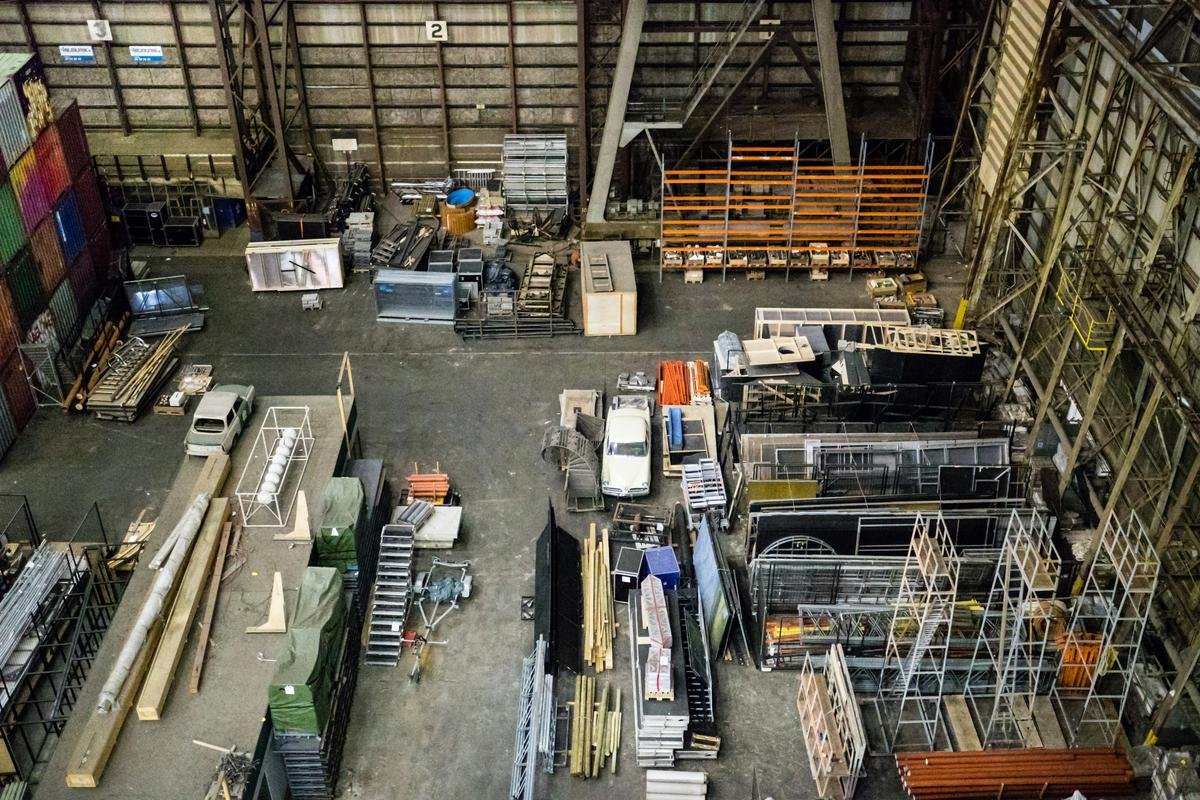
The Future of AI in Manufacturing
The augmentation of the manufacturing landscape through artificial intelligence (AI) represents an important shift towards an era of heightened efficiency, adaptability, and innovation. AI’s expansion into this sector indicates a profound evolution in the methods we, as a society, utilize to produce goods, maintain industrial equipment, and manage resources.
One aspect that portends to redefine the industry’s future is the enhanced potential for supply chain optimization. By wielding sophisticated algorithms coupled with extensive data inputs, AI can markedly refine forecasting accuracy for material needs and optimize logistics, thereby minimizing inventory excesses and shortages. This leads to a streamlined supply chain that deftly responds to market fluctuations and customer demands with unprecedented agility.
Simultaneously, AI’s foray into predictive maintenance heralds a significant downturn in unplanned machine downtime. By preemptively identifying potential faults and wear within machinery, AI forestalls breakdowns before they eventuate, ensuring continual production flow and reducing maintenance costs. This, in turn, extends the lifespan of valuable industrial assets and buttresses overall operational resilience.
Furthermore, AI will enrich the human-robot interface, facilitating a collaborative environment where cobots—robots designed to work alongside humans—will safely and efficiently complement human tasks. Implementing machine learning enables these cobots to adapt and refine their assistance based on iterative interaction, fostering a more dynamic and flexible workforce.
Design innovation takes a leap forward with AI’s generative capabilities. By employing generative design algorithms, manufacturers are empowered to explore an expansive design space, uncovering optimal configurations and material allocations to create lighter, stronger, and more efficient products. Such tools mark a departure from traditional design constraints, ushering in a new epoch of product development that is both more considerate of resources and more attuned to complex requirements.
To fully harness the capabilities of these advanced tools, the workforce must also evolve. AI and augmented reality (AR) or virtual reality (VR) together hold the promise of revolutionizing training and support. Through immersive learning experiences, workers can acquire new skills or troubleshoot complex issues in real-time, all within a controlled and informative virtual environment. This synergy promises to not only accelerate the learning curve for employees but also reduce errors and enhance safety standards.
However, the proliferation of AI in manufacturing does not come without its challenges. The pivotal role of data necessitates robust data governance and infrastructure to effectively feed AI systems. Compatibility with legacy systems remains an intricate hurdle, potentially requiring meticulous overhaul or thoughtful integration strategies.
The industry also encounters a widening skills gap that necessitates a comprehensive approach to developing AI-related competencies among the workforce. The pivotal need for professionals trained in data science, machine learning, and AI operation forms the backbone of an adeptly automated future.
Accompanying these technical and workforce considerations are imperative discussions surrounding security, privacy, and ethics. Safeguarding sensitive production data and ensuring the unbiased, fair, and ethically mindful employment of AI systems will be crucial in maintaining stakeholder trust and adherence to evolving regulatory frameworks.
Lasty, cost considerations cannot be overlooked. Investment in AI technologies behoves a careful examination of potential returns, with an eye towards scalability and long-term benefits that must outweigh the initial capital outlay.
In summation, while AI’s ascendancy in manufacturing ushers in unprecedented benefits, it also demands a conscientious and strategic approach encapsulating multiple facets of industry operation. Yet, given its manifold potential, AI stands not as an isolated technological leap, but as an integrative force poised to redefine the complexity and capability of manufacturing in the years to come. As the sector pivots toward this innovative horizon, the evaluative approach to these encompassing challenges will likely determine the depth and breadth of AI’s transformative impact.

Economic and Social Impact of AI in Manufacturing
Artificial Intelligence’s Influence on Workforce Dynamics and Environmental Sustainability in Manufacturing
As Artificial Intelligence continues to evolve, one observes a nuanced shift in workforce dynamics within the manufacturing sector. The implementation of AI necessitates a pivot from traditional labor-intensive roles towards more cognitively demanding positions that focus on managing and interpreting AI outputs. This transition not only alters the dynamics of employment but also necessitates an evolution in educational frameworks to prepare a workforce competent in AI. Educational institutions are now tasked with developing curricula that can bridge the skills gap, fostering a new generation of workers proficient in AI-supported environments.
Concurrent with changes in the labor market is AI’s contribution to environmental sustainability in manufacturing. AI enables enhanced resource management, leading to a reduction in waste and optimization of energy usage. Through intelligent algorithms, AI systems can predict the amount of raw materials required, thus minimizing excess and its associated environmental footprint. Additionally, by optimizing energy consumption during production, AI contributes to lower carbon emissions, a crucial factor in combating climate change.
Moreover, the integration of AI in manufacturing extends to product lifecycle management, offering significant opportunities for recycling and remanufacturing. Advanced AI systems can track and analyze the usage patterns and deterioration of products, informing decisions regarding when to recycle materials. This approach not only promotes a circular economy but also reduces the reliance on raw material extraction, which has extensive ecological impacts.
In contemplating the impacts of AI, the consideration of urban and regional planning becomes imperative. As AI-fueled manufacturing hubs grow, there is a need to strategically plan infrastructure to support these advanced facilities. This entails ensuring seamless connectivity for transport and data, as well as adequate utility services, to sustain AI-driven manufacturing ecosystems.
This close examination of the broader economic and social implications reveals that AI is not merely a tool for enhancing production efficiency but a catalyst for systemic transformation within the manufacturing sector. It is irrefutably reshaping the workforce, stressing the importance of lifelong learning and adaptability. Furthermore, it is serving as a cornerstone in the pursuit of environmental sustainability, enabling manufacturers to contribute to a greener planet. Finally, it underscores the necessity for strategic urban and regional planning to accommodate the burgeoning AI-integrated manufacturing landscape. The influence of AI is profound and all-encompassing, heralding a future where manufacturing is smart, sustainable, and intrinsically human-centric.

With the blueprint of the future drawn from the insights of today, artificial intelligence stands poised to redefine the landscape of manufacturing. As we gaze ahead, it is imperative to navigate this brave new world with both caution and curiosity, balancing the pursuit of innovation against the tapestry of ethical and social considerations. The evolution of AI within this sphere remains a testament to human ingenuity, symbiotically intertwining the ambition to progress with the wisdom to guide that progress responsibly. The journey thus far is only an early chapter in what promises to be an epic saga of transformation, characterized by an increasing symbiosis between human creativity and the precision of machines. May this exploration serve as a compass for the future, steering us toward a horizon where technology amplifies human potential and fosters a more efficient, equitable, and sustainable world.